Environmental Preservation
Utilization of Natural Resources / Reduction of Industrial Waste
Reduction Target of Industrial Waste
Accompanying the commencement of GD100 Phase III, we have revised the reduction target.
[Domestic Factories]
- Reduce the total quantity of industrial wastes in the three-year period from 2012 to 2014 by 35% compared to 2006
- Reduce the unit base for industrial wastes by at least 1% every year
[Overseas Factories]
- Reduce the unit base for industrial wastes by at least 1% every year
Our Target for Zero-Emission
We have been working so that more of our factories can achieve total zero-emissions within our group both in our domestic and overseas operation sites.
[Domestic Factories]
- Maintain a 100% rate of recycling resources at all factories
[Overseas Factories]
- By the final year of GD100 of 2017, achieve total zero-emissions at all overseas factories
Generated Amount of Waste Materials by the Group Domestically and Overseas
The generated amount of waste materials by the entire Group domestically and overseas was reduced by 0.3% year-on-year to 27,995 tons during FY 2013.
Generated Amount of Waste Materials by the Group Domestically and Overseas
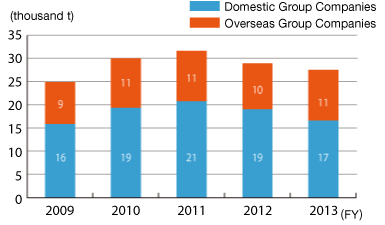
Our Addressing the Reduction of Industrial Waste
Generated Amount of Waste Material and its Unit Base at Domestic Operation Sites
The generated amount of waste materials*1 in FY 2013 resulted in 15,134 tons, an 11% decrease compared to FY 2012 (January to December) and we were able to improve the unit base of the generated amount of waste materials (per net sales) by 13% compared to FY 2012. During GD100 Phase III (FY 2012 to FY 2014) that began in FY 2012, we will work towards achieving the newly set target. We will continue working towards minimizing product scrap during FY 2014.
- *1
- Refers to any waste materials as a result of normal production activities including everything such as industrial waste, general waste, and valuable resources. Incidentally other than that, there were 2,611 tons of waste generated by the disposal of some facilities that are excluded from our target management in FY 2013.
Changes in Generated Amount of Waste Material and its Unit Base
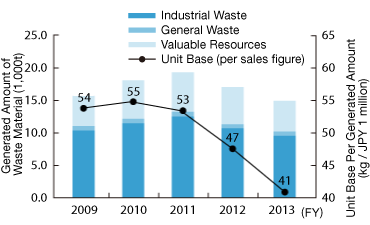
* This indicates the amount generated during the accounting years from 2009 to 2010 (April to March period).
The accounting period for the fiscal year of 2011 is from April to December. As such, data for the generated amount from January to March 2011 (fiscal year of 2010) has been added to this to provide a tally for the full calendar year.
For the amount generated during FY 2012, the generated amount for the accounting year lasting from January to December is displayed.
Achievement of 100% Recycled Resources from Industrial Waste of our Domestic Operation Sites
Since Yokohama Rubber has achieved Total Zero-Emissions*2 in all our domestic operation sites in March 2006, we have been working on "100% recycled resources*3 from our industrial waste".
As a result, we were able to achieve our target of "recycling 100% of our industrial waste into resources" in all our domestic operation sites in the fiscal year of 2009.
We maintained this in the fiscal year of 2013 as well; we will continue to do likewise from the fiscal year of 2014 onwards.
Furthermore, incineration was completely suspended and internal treatment abolished at the Mie Plant, and all of these operations were outsourced.
*2 Definition of total zero-emissions: not generating any direct landfill disposal at all.
*3 Definition of 100% recycling resources is not to leave any disposal (= direct landfill disposal + incineration amount of the materials without any useful purposes) until the end.
Flowchart of Industrial Waste Disposal (FY2013)
Promotion of Zero-Emissions at Overseas Operation Sites
We are promoting activities aimed at achieving complete zero-emissions status at our overseas production sites in order to promote environmental activities that are consistent with our approach taken in Japan.
As a result of these efforts, thus far five of our production sites in Asia have achieved complete zero-emissions status. Although no additional productions sites achieved complete zero-emissions status in the fiscal year of 2013, we investigated issues primarily at our production sites in the United States and promoted initiatives aimed at attaining this status. In the fiscal year of 2014, we will continue with our efforts to increase the number of production sites that have achieved the status of complete zero-emissions.
Management of Proper Disposition with Waste Disposal Contractors
In order to prevent any case of unlawful disposal such as unauthorized dumping, every year we are conducting onsite audits based on Yokohama Rubber's own auditing standard. We have conducted 95 cases of audits in the fiscal year of 2013 in total. As a result, we were able to confirm that all our contractors are handling our disposal in the proper manner.
Storage and Disposal of PCB-Containing Waste
We are properly storing and disposing of used machines that contain PCB such as transformers or condensers in accordance with our national legislation (Law Concerning Special Measures against PCB Waste).
In the fiscal year of 2013, we had completed the disposition of two machines in total at domestic group companies that contain high concentrations of PCB. From fiscal year of 2014 onwards, as for our machines that contain PCB registered in advance, we will continue to store them properly and wait for the notification of availability for disposal.
In addition, estimates are being acquired for the treatment of other machines owned that contain low concentrations or traces of PCB.
Five machines were treated during FY2013.
Consideration towards Raw Materials for Product
Increasing the Ratio of Regenerated Rubber Used
The Yokohama Rubber Group is actively working to effectively utilize recycled raw materials and increase the use of various forms of regenerated rubber in its tires.
Three types of recycled rubber: rubber powder, reclaimed rubber, and rubber reclaimed from our rubber trash are used as rubber recycled materials.
The percentage of purchased raw materials accounted for by rubber recycled materials was 0.8% for the entire group (1.1% for domestic business locations and 0.4% for overseas business locations). We aim to improve formulation technologies and rubber blending technologies in an aim to increase the usage rate of rubber recycled materials overseas.
Regenerated rubber powder is recycled rubber in a powdery state created by pulverizing waste tires, which are typically used mainly for heat. This regenerated raw material greatly contributes to resource conservation and resource recycling. Conventionally, it has been difficult to use regenerated rubber powder in tire applications because the particle size has been large, leading to a weaker physical property when combined with rubber. However, Yokohama Rubber has established a compounding technology that improves this physical property by blending rubber with finely ground regenerated rubber powder. We began mass producing tires with this blend of rubber and regenerated rubber powder in February 2009. Over the last five years we have expanded our use of regenerated rubber powder and as a result increased the ratio of regenerated rubber used in our tires by 2.7 times compared to 2008.
Currently, we are utilizing regenerated rubber powder in various compounds found mainly in PC, TB, and OR tread liners manufactured at our plants in Japan, the United States, the Philippines, Thailand, Vietnam, and China. We are working to improve the level of our blending technologies and actively striving to expand the compounds that can be blended with regenerated rubber powder.
Since first using regenerated rubber powder at a plant in the United States in 2006, the Yokohama Rubber Group now uses an amount equivalent to 910,000 waste tires, as calculated by a major regenerated rubber powder manufacturer. This is equivalent to saving some 50,790kl of crude oil and 163,516 thousand kWh of electricity. This also means that we have been able to reduce some 22,400 tons of CO2 emissions into our atmosphere.
We plan to promote the manufacture of tires with regenerated rubber powder at our new or expanding overseas production sites as part of our commitment to effectively utilize recycled raw materials on a worldwide scale.
Resources Circulation by Using Regenerated Rubber Powder
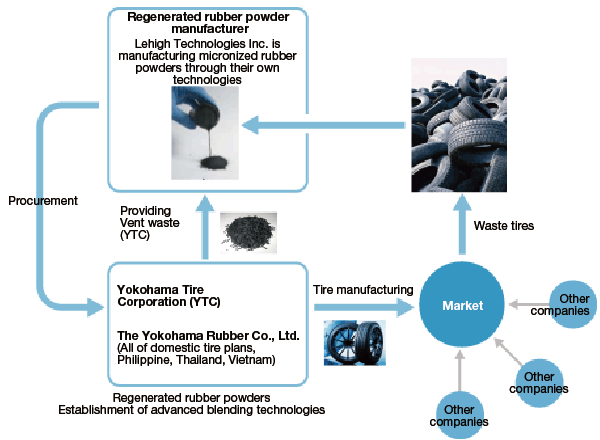
Environmental Impact Reduction Effect from the Use of Regenerated Rubber*1
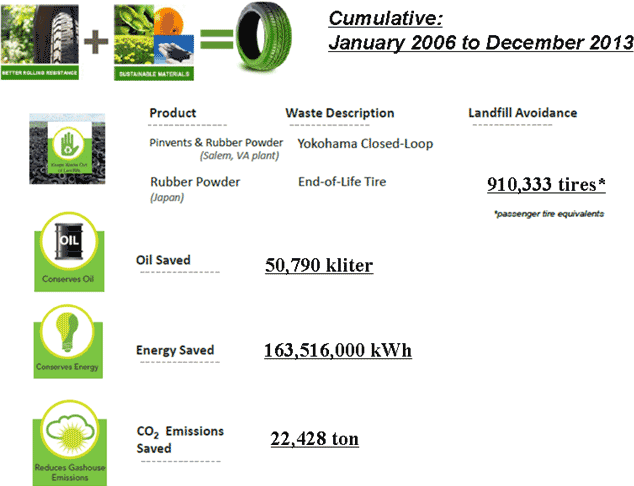
Changes in Usage Ratio of Regenerated Rubber*2
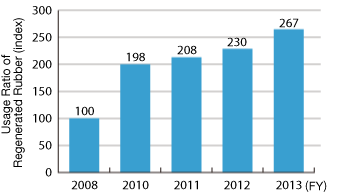
*1: Data provided by Lehigh Technologies
*2: Ratio of new rubber consumption based on results of acceptance inspections
Addressing Cases in the Fiscal Year of 2013
Reuse of Used Vulcanized Bladder as Raw Materials
In 2007, we commenced our internal mass production at domestic plants of used vulcanized bladder*, establishing for the first time in the industry recycling technologies for recycling to a state close to unvulcanized. As recycled rubber of a higher quality than that gained through conventional technologies can be produced with twin axis screw extruders installed in processing facilities, one of the strengths of this technology is that it allows this rubber to be used as a raw material for tire products, etc. without compromising their quality.
As for tire products, we are using these materials mainly for tires for passenger cars and as materials for truck and bus tires. Meanwhile at plant in the US, studies have been conducted over several years concerning the provision of used vulcanized bladder to recycled rubber powder manufacturers and to use this pulverized recycled rubber for tire products. There are plans for practical application in the near future.
Also, regenerated rubbers available in the market are to be used more widely other than tire products such as a part of raw materials of industrial rubber products like conveyor belts; we are also considering their deployment for the tires of construction vehicles. We will continue to expand their usage by applying them to tire products and rubber products from now on.
* Bladder: Refers to sub-material made of rubber to be used during vulcanization process of tire manufacturing; it will be blown like a balloon to press tires from inside onto the mold.
Twin axis screw extruders
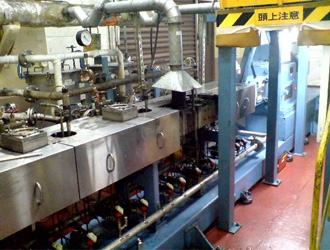
Consideration towards Water Source
Total Water Withdrawal Amount Overseas and in Japan
In the fiscal year of 2013, our total water withdrawal amount from water source resulted in 8,380,000 m3 both in our domestic and overseas factories. The breakdown is 6,900,000 m3 from domestic operation sites and 1,480,000 m3 from overseas operation sites.
Total Water Usage, Usage of Reused and Recycled Water, and Water Circulation Rate
In the fiscal year of 2013, total water usage in our domestic operation sites resulted in 76,100,000 m3; the breakdown is 6,920 m3 for the usage amount of reuse and regeneration and 6,900,000 m3 for water withdrawal amount; the water circulation rate was as good as 90.9%.
Addressing to Reduce Water Withdrawal by our Domestic Operation Sites
In the fiscal year of 2013, with anticipation of a 1% improvement in the unit base from the results of FY 2012 we developed our activities by targeting 6,940,000 m3; consequently, we were able to achieve our target by a small margin with 6,900,000 m3, which is a decrease of 7.5% year on year. The breakdown of water withdrawal from water source in the fiscal year 2013 was 460,000 m3 for clean water, 1,120,000 m3 for river water withdrawal, 60,000 m3 for industrial water, and 5,260,000 m3 for well water withdrawal.
Primary Actions for Water Resource Preservation
- Usage of the circulated facility cooling water
- Collection of steam condensate from vulcanization process
- Conduct overflow prevention of our reservoir tanks
- Conduct water leak prevention measure of underground piping
- Ensuring of daily inspection and patrol and repairing leaking points
-
Changes in Water Withdrawal Amount at our Domestic Operation Sites
-
Breakdown of Water Withdrawal Amount from Water Source in the Fiscal Year of 2013
(Unit: million m3)
Addressing to Reduce Water Withdrawal by our Overseas Factories
In the fiscal year of 2013, with anticipation of a 1% improvement in the unit base from the results of FY 2012 we developed our activities by targeting 1,560,000 m3; consequently, we were able to achieve our target with 1,480,000 m3, which is a decrease of 5.2% year on year. The breakdown of water withdrawal from water source in the fiscal year 2013 was 1,480,000 m3 for clean water and 1,000 m3 for well water withdrawal.
Changes in Water Withdrawal Amount at our Overseas Operation Sites
Implementation of the water risk assessment
WRI Aqueduct conducted a water risk assessment on the areas where our domestic and overseas business locations are located to confirm our water risk level. While it was confirmed that domestic production bases are located in areas with relatively low water risks, water risks were assessed as high in China and the Philippines. Based on these water risk assessment results, we plan to make even more active efforts to use water resources efficiently and respond to the risk of water-related disasters.