Together with our Customers
Assurance of the Safe MB Products
Basic Notion of the Activities for Quality Assurance
In the MB Division, our basic policy is that “We will contribute to society by planning, designing, producing, and selling attractive products for the satisfaction of our customers while maintaining a quality assurance system in all of our processes, including service.”
By putting the reassurance and safety of secondary, tertiary users, and every consumer’s life being surrounded by products from our MB Group over the satisfaction of our primary customers that are mainly manufacturers, we make efforts to strengthen our quality assurance system on a daily basis.
MB Group – Mid and Long Term Approach Guidelines as to Quality Assurance
We will raise customer credibility by continually providing high quality products all the time.
In order to gain customer credibility, we will ensure:
- Customer-centric systematic quality management and product development
- Effectuation of quality control system and continuation of autonomous quality improvement activities
(1)Attainment of zero complaints outflow
(2)Operation of quality management system (introduction of the system in new locations, businesses at ease) in consideration of QCD (quality, cost, delivery). - Preparation of crisis management system and continuous correspondence to it
- Continuation of customer-centric technical service activities
- Global development of above mentioned guidelines
Our Approaches for Quality Assurance
Work Operations by our MB Group
Our MB Group is dealing with various commodities for mainly hoses and couplings, industrial products, adhesives and sealants, and aerospace products. Our mainstay products are industrial rubber products such as various hoses and conveyer belts, adhesives, various sealing materials, fuel tanks for aircraft, lavatory units and more; our major customers are the manufacturers of automobiles, construction equipment, air frames, vehicles, industrial facilities, public corporations, and construction companies. Our products will be delivered to our customers through our distribution companies and agencies. In addition to those B-to-B products, we are manufacturing various B-to-C products as well, such as golf goods.
As for those products, we will ensure safety assurance through incoming goods inspections for raw materials to use, half-finished goods inspections such as blended rubber materials, product inspections for final products; we are also trying to secure quality with their design by conducting designing screening from the stage of product planning, the stage of designing, and the stage of process designing. Note that risk assessments (environmental and product assessments) are conducted for all MB products.
Lecture classes related to customers’ correspondence in our company
In “Industrial Technology & Sales Department” which was launched in June 2009, experienced engineers with products knowledge related to industrial materials, HAMATITE, hose plumbing stay at each representative sales company. We implement activities to develop human resources and enhance communication at sales companies and locations in an aim to provide prompt customer support in the field.
34 lecture classes were held in fiscal year 2013 (from January to December)
Note that organizational changes were conducted at the end of March 2013 so that both the head office functions and quality assurance and service departments would be integrated throughout the Group under quality assurance supervision that goes beyond boundaries of product types.
In an aim to further improve the customer satisfaction of mining-related customers (conveyor belts and tires for construction machinery vehicles) and port-related customers (marine hoses, fenders, and tires for industrial vehicles) that are the shared customers of industrial products divisions and tire divisions, mutual product study meetings and information collection activities were implemented by these divisions from the summer of 2013 in an effort to share market information.
Approaches for our Customers
New company “Yokohama Rubber MB Japan” was launched in October 2010, Integrating a part of function in MB sales companies and industrial products marketing department of our head office. With this, we integrated marketing power of sales companies which were close to our customers and back up function of manufacturers, and have introduced system development with a feeling of identification and swift decision making. We deploy a staff member from quality assurance department of a manufacturing company, who improves consciousness of product quality of our staff during the course of lecture related to product quality to our sales staff members, and are working to continuously provide our customers with safe and high quality products.
Flow Chart of our Customer Feedback and its Process
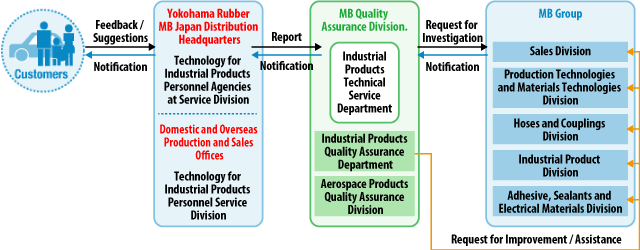
Our Internal Activities for Quality Assurance
1. Risk Management – Dealing with Customers
We aim to clarify rules, standardize through documentation, and equalize processes in order to create a Group-wide quality framework that always gives consideration to quality maintenance and improvement from the customer’s point of view for the various sales routes of a wide variety MB products.
Also, in the event of any quality issues or complaints in the market over our products already delivered to our customers, not just we act promptly to solve the problems, but also we take actions to avoid any recurrence. As for preventive measure for recurrence, we will verify its validity by conducting quality audit on a regular basis whilst checking whether corrective measures are duly conducted.
Also, we have our framework called the "Meeting for Product Improvement" where relevant divisions get together to lead to product improvement based on quality information in the market not to allow any quality issue to occur. We are aiming for the improvement on CS by relevant divisions to get together through this framework.
2. Activities on Quality Improvement – Framework to be in place to maintain customer credibility
Our MB Group has formed their activities on quality improvement by reflecting their mid and long term guidelines to facilitate their activities.
- We are continually making improvements based on the verification of international quality management systems such as "ISO/TS-" per sector. Our Industrial Products Business Group has obtained this certification by establishing quality assurance supporting system with more clear regulations and structures as to their operational responsibility at our Technology, Production, and Sales Division; upon integration and organizational shifting based on their functions as Industrial Products, Adhesives and Sealants, and Hoses and Couplings Businesses.We continuously acquire certification of “ISO/TS-” at our overseas production bases as well.
Acquisition of “ISO9001, ISO/TS16949” at our production sites in Japan and overseas (year and month of the latest update)
Production sites ISO9001 ISO/TS16949 Domestic Ibaraki Plant April 2014 February 2013 Nagano Plant April 2014 February 2013 Adhesives and Sealants (HAMATITE)Plant April 2014 - Ibaraki Plant April 2014 - Industrial Products Plant April 2014 - Overseas Yokohama Industries Americas Inc. DIV.1 - October 2012 DIV.2 - September 2012 DIV.3 - February 2013 Yokohama Industries Americas Ohio Inc. DIV.4 January 2014 - DIV.5 August 2013 - SHANDONG YOKOHAMA RUBBER INDUSTRIAL PRODUCTS CO., LTD. August 2011 - YOKOHAMA HOSES & COUPLING (HANGZHOU) CO., LTD. May 2012 - YOKOHAMA HAMATITE (HANGZHOU) CO., LTD. August 2013 - SC KINGFLEX CORPORATION March 2014 - YOKOHAMA RUBBER (THAILAND) CO., LTD. (YRTC) HOSES DIV. April 2012 March 2012 Adhesives and Sealants(HAMATITE) DIV. April 2012 -
Our internal audit and examination activities have been conducted throughout all the plants, technical divisions, and overseas operation sites of MB Group; we are trying to facilitate to raise awareness of quality and activities for improvement including "Quality Examination by our Top Executives" conducted by our Directors. Also, for the purpose of fortifying our quality framework, we are promoting the obtainment of qualifications as internal auditor; about 326 employees have obtained this qualification at the point of March 2014.
3. Fortification of Global Quality Assurance Supporting System
MB Group has overseas operation sites in North America, China, Taiwan, and Thailand. We are expanding our activities by aiming for our universally common quality standard by summarizing various rules on quality assurance activities, by making clear about the authorities on responsibilities between overseas operation sites and relevant domestic divisions from product planning to quality assurance supporting system after sale. Enlightenment materials for quality for both expatriate staff and local staff are duly utilized in all our operation sites.