Together with our Customers
Assurance of the Safe Tire Products
Basic Notion of the Activities for Quality Assurance
The basic notion of our quality assurance activities at the Tire Group is expressed under the "Quality Guidelines" in accordance with Yokohama Rubber's Corporate Philosophy; "We will enrich people's lives and contribute to their happiness and wellbeing by devoting our wholehearted energies and advanced technologies." We are continually working on our daily operation with quality assurance based on these quality guidelines.
Quality Guidelines
- We will continually provide quality products so that our customers from all over the world can purchase with confidence followed by their sense of satisfaction. We will thereby grow as a corporation and contribute to society by maintaining proper profits through not just customer satisfaction, but also winning their sense of trust afterwards.
- We will continue to make improvements on our activities of the entire process of Tire Group in order to meet our customers' requirements, as well as to comply with the entire regulations related to all the products we provide, plus any requirements of the quality management of ISO9001 and ISO/TS16949 by aiming for the establishment of even better corporate structures.
- In order to realize these quality guidelines, each division will set forth their own quality targets, review their status, followed by ensuring their achievements.
- We will get all our relevant directors and employees thoroughly familiarized with these quality guidelines.
Our Approaches for Quality Assurance
Our Approaches for Customer Service
We swiftly share the product information given by our customers to the respective sections in our company. We always develop our business activities to meet our customers’ expectations, promptly solving issues indicated by our customers coordinating with our related sections.
Flow Chart of our Customer Feedback and its Notification
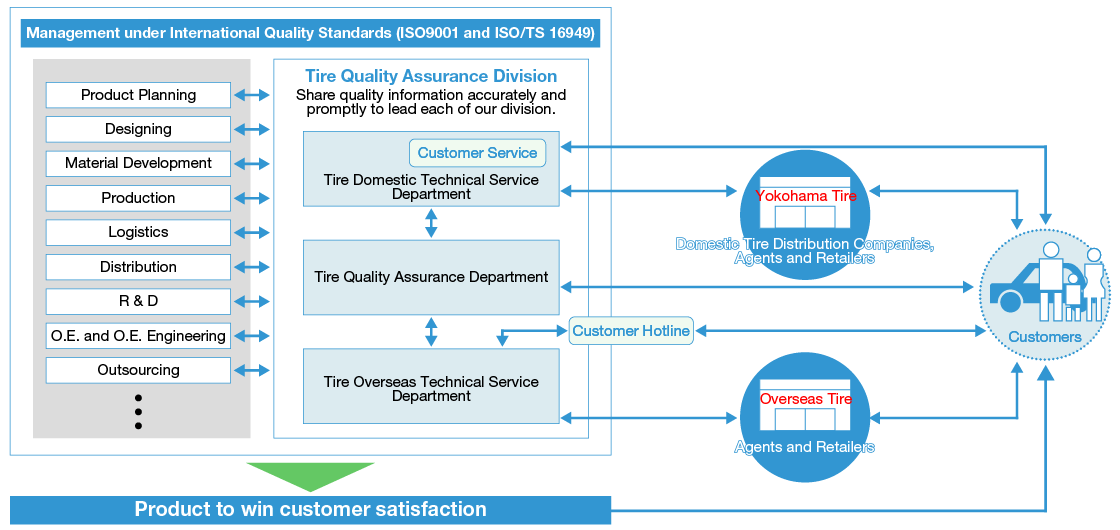
Thin arrows in the diagram refer to information flow; the thick arrows refer to the providing flow.
Activities for Quality Assurance
- Approaches for ISO9001, ISO/TS16949 (Establishment of Quality Management System)
The basis of the supporting system of quality assurance in automobile industry is to comply with ISO/TS16949. This is the quality management system standard required by major automobile industry which is a prerequisite in order for us to develop our various businesses on a global scale. So far, our three domestic plants, plus five overseas plants in which tires for passenger cars, trucks, and buses have obtained preceding certifications are manufactured; we are about to expand this on a global stage. Also, we are proactively facilitating so that our managerial level of supervisors of each division can obtain qualification as internal quality auditor; we have newly certified 112 personnel in the fiscal year of 2013 through our various training sessions and seminars (total number of certified personnel: 826).
Status of Certification Obtaining as to International Quality Standards (the Latest Year/Month for Renewal)
ISO9001 ISO/TS16949 Domestic Mishima Plant June 2012 Aug. 2013 Shinshiro Plant June 2012 June 2012 Mie Plant June 2012 June 2012 Onomichi Plant June 2012 - Overseas Yokohama Tire Corporation Dec. 2012 - Yokohama Tire Philippines Inc. May. 2011 May. 2011 Yokohama Tire Manufacturing (Thailand) Co., Ltd. * June 2012 June 2012 Yokohama Tyre Vietnam Inc. Dec. 2011 - Hangzhou Yokohama Tire Co., Ltd. Oct. 2012 Oct. 2012 Suzhou Yokohama Tire Co., Ltd. Apr. 2012 Oct. 2012 - Improvement of the Support System of Quality Assurance from the Perspective of our Customers
In order to improve our supporting system of quality assurance, we are trying to leverage the level of our quality system aiming for the solution for any issues being identified from our customers' perspective through our internal quality audit.
- Conducting Quality Examination by our Top Executives
We believe that any activities on quality improvement can be achieved only through high awareness of our top executives including our President in order to motivate our workers at our various operation sites; further actions for improvement could even accelerate and fortify it. Therefore our company is conducting "Quality Examination by our Top Executives" to examine annually each of our plants and divisions by our management team.
- Improvement on the Performance Level for Plant Supervisors
In order to fortify our strength at operation sites, our Tire Global Quality Assurance Division is continually conducting Enlightenment and Training Programs by focusing on the quality of each hierarchy, primarily plant supervisors, to improve our overall quality level at all our plants. We will provide new training for supervisors at overseas plants during FY 2013 as we respond to globalization.
- Quality Assurance Activities Related to Development Operation
We are striving to deliver products with quality assurance by conducting Design Reviews to evaluate achievements for each step from product planning, designing, to production. Also we follow up with our customers how much they are satisfied after sales, followed by feedback to our development operation team in order to develop and provide even better products all the time.
- Safety Assurance through the Entire Life Cycle of Tires
In order for our customers to continue to use our safe products comfortably, we handle promptly in the event of any incident that may cause inconvenience to our customers such as product recall by notifying to our customers as soon as possible.
- Group-Wide Quality Problem Recurrence Prevention Briefing Session
As an initiative aimed at improving the awareness of all employees towards quality, the Group-Wide Quality Problem Recurrence Prevention Briefing Session was held jointly by tire and MB divisions. We will continue to hold these sessions during FY 2014.
Our Approaches for our Domestic Tire Service
Basic Notion of the Activities for Domestic Services
The basic guidelines as to quality of our Tire Group are set forth in our "Quality Guidelines". Tire Domestic Technical Service is always developing service activities from our customers' perspective in order for them to duly satisfy with our products and establish a sense of trust according to those guidelines.
Supporting System of our Services (Domestic)
In order to facilitate obtaining highly-accurate market information and prompt action in case of any defect of our products, our supporting systems are already in place as follows:
- We have placed our personnel from the Tire Domestic Technical Service Department in six cities nationwide in Japan (Sapporo, Sendai, Tokyo, Nagoya, Osaka, and Fukuoka).
- We have formed our service network by operating our qualification system (YFS = YOKOHAMA FIELD SERVICE)* applicable to our regional distribution companies and sales offices in Japan (358 nationwide).
- We are holding seminars and reporting sessions for our regional distribution companies and sales offices to introduce our new products, develop our service guidelines, and share some market information.
- * Qualification system (YFS = YOKOHAMA FIELD SERVICE) refers to our system to grant qualifications to eligible personnel as to product knowledge, prompt response to customer complaints and so on upon training and testing at our seminar organized by the Tire Domestic Technical Service Department. There are 814 individuals who possess this qualification at the point of fiscal year of 2013. There were 28 new YFS personnel that acquired qualification during FY 2013.
Assignment of at least one service staff member at each business location (target value: qualification received by new sales managers: 100% achievement).
Note that the target for FY 2014 is 20 staff members.
Obtaining Market Information and Application to our Products (Domestic)
We have our framework in place to obtain and analyze customer feedback and market evaluation, develop them internally, and apply them into our next products in order to provide products to ensure we win continual customer satisfaction.
1. Obtaining Market Information (Domestic)
Our personnel from Tire Domestic Technical Service Department are conducting hearings from our customers and surveys of actual tires based on the information from our distribution companies. The gathered information will be developed internally as Technical Correspondence to improve the performance of our products and apply it into our next products as well. 628 pieces of correspondence were issued in the fiscal year of 2012, in contrast to 587 in the fiscal year of 2013.
2. Development of Gathered Information at our Customer Service
Changes in the Number of Cases Directed to our Customer Service
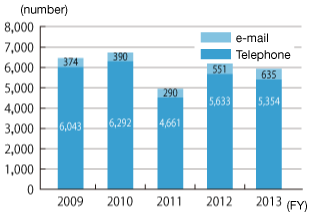
- *The number in 2011 is from April to December.
Our Customer Service team stationed in our headquarters is handling customer inquiries as to tires including obtaining information such as market evaluation or complaints as to our products. They are dealing directly with our customers through telephone or e-mail, followed by developing such precious information gathered throughout the company in a prompt manner. This is to help improve our product performance, catalogue, and our homepage. Also, we gather and analyze information from our customers, or for any information related to quality issue, followed by reporting internally to apply them into our next product.
3. Holding Reporting Sessions for Customer Satisfaction Survey (CS Reporting Session) of our New Products (Domestic)
We are obtaining and analyzing market evaluations as to our new products by holding CS Reporting Sessions together with our Development Division to apply such information into our next products. We held such sessions five times in the fiscal year of 2013.
Flow Chart of our Market Adaptability Verification
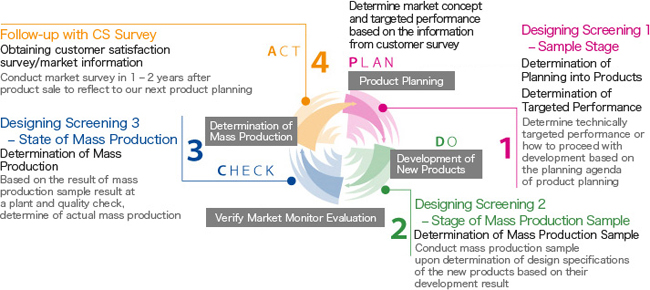
Market Enlightenment Activities – Customer Seminar (Domestic)
We are conducting various activities that will lead to customer satisfaction; as we hope that we could draw more interest and attention from many of our customers into tires by enlightening them with proper usage of tires. We have conducted such Customer Seminars 48 times in the fiscal year of 2013.
Filling Operation of Tire Air – Special Seminar
It is required by law to conduct special seminars and so on under Ordinance on Industrial Safety and Hygiene (Ministerial Order by Department of Labor) towards the workers who are involved in the filling operation of tire air. Yokohama Rubber is conducting various seminars in accordance with our regulations conducted by our personnel of Tire Domestic Technical Service Department or employees at our distribution companies who are qualified as a lecturer for Filling Operation of Tire Air – Special Seminar mainly for our valued customers from Tire Distributors and Transporting Companies.
Seminars for Drivers (Mainly our Valued Customers from Bus Companies and Transporting Companies)
We are conducting various seminars as to basic knowledge of tires plus daily inspection and maintenance work in order for professional drivers, i.e. our valued customers who deal with precious passengers and cargoes, to keep making improvements with their safety driving, economical driving, and quality transportation.
These days since we have noticed that many of our valued professional drivers are more inclined to be concerned about environmental issues and various approaches on cost cutting, we are bringing up the relativity of tire and fuel efficiency as well.
Sample of the Materials from Filling Operation of Tire Air - Special Seminar
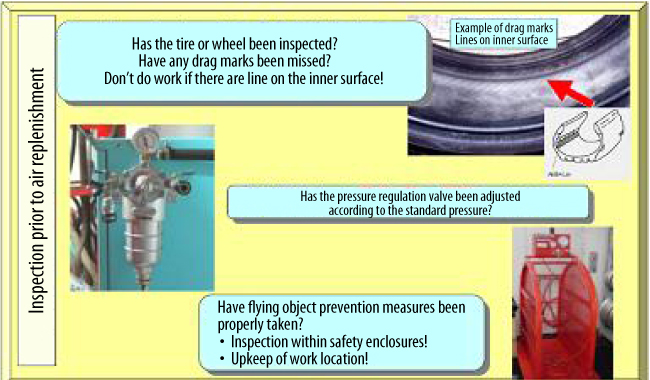
Document of our Seminars for Drivers
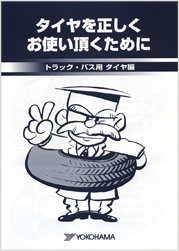
Acquiring Market Information and Incorporating it in Products (Overseas)
In the same manner as in Japan, we improve market quality by acquiring quantitative data, analyzing information from each region, and incorporating this information in new products.
Expansion of our Global Service Network (Overseas)
We are conducting the below-mentioned measures in order for our customers located all over the world to be able to use our products with a great level of satisfaction as we expand our global service network.
- We have placed our Technical Service Personnel in each of our regional business locations in North America, China, Europe, Asia, Central and South America, Middle East, and Africa.
- We have established the network by technical staff from each distribution companies and agencies under our regional sites. This is to provide our technical service to each country all over the world excluding Japan.
- Obtain highly accurate information as to product usage and requirements from our products for each region and country.
Collecting market information
Information that has been collected for each region and country is analyzed and utilized for making better products by means such as improving existing products and planning new products.
In addition, because usage conditions for vehicle tires for construction and industrial use vary considerably depending on the customer, we select and recommend tires suitable for customers after researching the use environment of each customer.
Customer information for vehicle tires for construction and industrial use
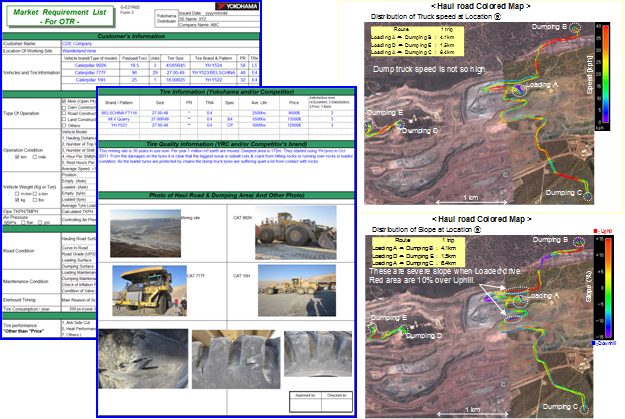
Training for service engineers
Establishment of the Tire Service Training Center in Thailand
Service engineers engage in technical services such as the collecting of market and qualify information as well as technical information initiatives designed to further increase customer satisfaction. As part of efforts to enhance Yokohama service engineer training throughout the world, a Tire Service Training Center was established in Thailand in October 2011. This tire training center is a facility for producing service engineers capable of engaging in practical service provision, as much as possible from the perspective of customers. In addition to learning basic knowledge and the latest information concerning tires, by learning tire manufacturing methods at a factory to gain a deeper understanding of tire structure and participating in an actual vehicle research program using a test course for a first-hand experience of tire and vehicle characteristics, participants are able to actually experience a variety of issues under various use conditions and learn how to make improvements. Training was conducted for 43 service engineers from 32 countries during the FY 2013 as the third year of the program. During FY 2012 we conducted training for 62 service engineers from 28 countries. As a result of receiving this training, it has improved the abilities of engineers to utilize the information system using the web as well as the accuracy of information.
Training for service engineers
Training surrounding vehicle tires for construction and industrial use
For 10 service engineers from 7 countries around the world engaged in sales and technical services surrounding vehicle tires for construction and industrial use such as on construction sites and in mining operations, during FY 2013 the production plant in Onomichi was the location of highly specialized training session covering the range from manufacturing processes to design methods and knowledge, as well as analysis techniques using actual tires as study materials. Through this training that improves capabilities to gather customer information onsite and tire analysis skills the Company continues in its efforts to enable system engineers to provide the high technical service levels that match and satisfy the requirements of customers for vehicle tires for construction and industrial use.
Training surrounding vehicle tires for construction and industrial use
Quality information aggregation system
The information gathered through the quality information system that was initiated in 2010 has been analyzed and applied to the establishment of better products, through means such as improvements to existing products and the planning of new products.
Information Collection System Using the Internet
Collection of Customer Information for Vehicle Tires for Construction and Industrial Use
Usage conditions for vehicle tires for construction and industrial use vary considerably depending on the customer. We collect information on individual customers in order to select and recommend