























|
 |




新タイヤの開発は必ずしも順調に進んだわけではなかった。
「従来の合成ゴムタイヤなら試作を繰り返さなくてもある程度狙った結果が出せる。しかし今回はそうはいかなかった。普通なら1回か2回の試作でうまくいくはずが、3回、4回と試行錯誤が必要になったり、これで大丈夫だと思ったところがうまくいかなかったり。正直、もうダメかもしれないと思ったこともありました。しかし最後は、チーム全員のやる気に賭けた」と野呂はいう。
開発チームは毎月のように少しずつ組成を変えたゴムを作成し、タイヤを試作しては茨城のテストコースに足を運んでデータをとった。その甲斐あって設定していた期限を目前にして目標性能に到達。ころがり抵抗を20%減らしながら、グリップ性能の目安となるウェット路面での制動距離においてもベンチマークのDNA dB ES501より優れた数字を出すことに成功したのである。
オレンジオイルを配合した天然ゴムベースの新コンパウンドは「スーパーナノパワーゴム」と名付けられ、新タイヤ「DNA dB super E-spec」の最大の特徴として打ち出すことが決まった。プレス発表も行い、あとは量産に入るばかり。ところが本当の修羅場はまだこの先に待ち受けていたのである。




2007年の1月から工場において新タイヤの生産が始まった。
「まず問題が出たのは原材料を混合する工程。思ったようなゴムができないんです。今回の製品は、材料から新しいものだったので、あらゆる面でこれまでとは違う細かい制御が必要でした」と新城工場技術課の秋山一郎は話す。作業手順を見直してマニュアルを新しく作ったり、一部の設備は新タイヤ専用に改造を加えたりしたという。
タイヤは、路面と接するキャップトレッドのほかにも、タイヤの骨格となるカーカス部、これを補強するための金属を編み合わせたベルト部、ホイールとの接合部となるビード部、そして空気を保持するインナーライナーなど、さまざまなパーツが貼り合わされて成形される(※2)。その製造の工程において、新素材のインナーライナーである空気透過抑制フィルムの貼りあわせの難しさが、またメンバーを悩ませた。
「成形工程では、円筒状にしたパーツを組み合わせて、内側から風船のようなもので膨らませて成形しますが、加硫により化学反応をおこし、タイヤとして完成するまでは、各パーツは疑似接着しているだけ。空気透過抑制フィルムは非常に薄いものの、元の形に戻ろうとする力がゴムよりも強いため、加硫工程の前にはがれてしまうことがあるという難点がありました。」(秋山)
次々と出てくる問題に対し、開発メンバーと生産メンバーが協力しあって解決策を探り、材料仕様の変更や製造方法の改善などを行って一つ一つ克服していった。そして最後には完成したタイヤの1本1本を細かくチェックして出荷したという。
「画期的な製品を作ろうと思えば多少のトラブルはつきものですが、この『DNA dB super E-spec』の大変さは格別。皆で苦労を乗り越えて作り上げたこのタイヤは、自分にとっても特別なタイヤになりました」(野呂)
※2 「タイヤの製造」についてはこちら

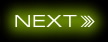
|
|
|