























|
 |




今回、野呂たち開発チームは、石油外資源比率80%という目標をクリアするための課題を大きく二つ設定した。一つはタイヤに占める重量比率がおよそ30%と大きいキャップトレッドの石油外資源比率を98%以上にすること、もう一つは重量比率で10%程度を占めるインナーライナーの重量を現状の1/5とすることである。
インナーライナーに関して野呂には一つのアイデアがあった。それは、「空気透過抑制フィルム」の採用である。「空気透過抑制フィルム」とは、横浜ゴムが独自開発をした、ゴム素材が持つしなやかさと空気漏れを効果的に抑制するプラスチック素材の特性を併せ持つ新素材。
「当社の空気透過抑制フィルムは、従来のライナーの5分の1の薄さで2倍の空気透過抑制能力があります。タイヤの重量を3%程度軽量化することで燃費向上に貢献するとともに、空気漏れを効果的に防いで空気圧を適正に保つことで燃費悪化を抑制します。」
この新素材のインナーライナーは、このとき世界各地の拠点で、試作タイヤによる性能や安全性のテストを繰り返し、実用化へ向けた確認をしているところだった。
「今回は環境性能を追及する当社のフラッグシップモデルで、コストの制約も少ない。高性能なこのフィルムを市販タイヤに採用する良いチャンスだと思い、決めました」と野呂はいう。



そして、前述したもう一つの課題、すなわちキャップトレッドの石油外資源比率を98%以上にすることについてはどうするか。
タイヤ用のコンパウンドは使用する部位の特性に合わせて、合成ゴムと天然ゴムが組み合わせて使われているが、高いグリップ力と耐摩耗性が要求されるキャップトレッドには、特性を出しやすい合成ゴムや石油系の配合剤が多く使われてきた。
天然ゴムは合成ゴムに比べて摩擦力が小さいため、これをキャップトレッドに使えば、ころがり抵抗は減少できる。しかしそのままではグリップの弱いタイヤになってしまう。天然ゴムならではの低いころがり抵抗を維持しながら、必要なグリップ力を引き出すためには、天然ゴムの性質をコントロールする新しい技術が必要だった。
「選択肢は二つありました。一つは末端変成という方法ですが、既に同じような技術を使った製品が存在していた。もう一つは、まだどこも手がけていない全く新しい方法でした」
どちらを選ぶか。前者の方法についてはある程度技術的な見通しは立っていた。一方、後者はほとんどゼロに近いところからのスタートになる。しかし野呂は新しい方法に賭けてみることにした。「せっかく新しく出すのに、他社技術の改良版と見なされては面白くない」と思ったからだ。

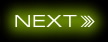
|
|
|