Together with our Employees
Safety and Health in Workplace
Basic Guidelines
Health and Safety are the basis of all our activities.
We aim to prevent any occupational injuries, create a pleasant workplace and overall health for our workers under the strong leadership of our managers and supervisors, along with our entire group’s employees’ cooperation of this matter.
Supporting System of Safety and Health Management
In Japan, we formed the "Safety and Health Sub-Committee" per division and workplace and the "Office-Wide Safety and Health Committee (legally stipulated)" per office under our Central Committee of Safety and Health that is headed by the CSR Department Manager. Activities on safety and health are an important approach common in companies and unions. Through interaction with the Japan Rubber Manufactures Association and Japan Rubber Workers Union Confederation to share safety information with other companies and other union confederation members, we are also trying to facilitate those by labor and management sides getting together. We also share our activities with our subcontractors by having them join their respective committees. As for our various overseas offices, they have their own supporting system in place according to the prevailing law under their country's governance. Safety and Health Management Department manages activities on safety and health in both Japan and overseas.
Our Supporting System of Safety and Health Management
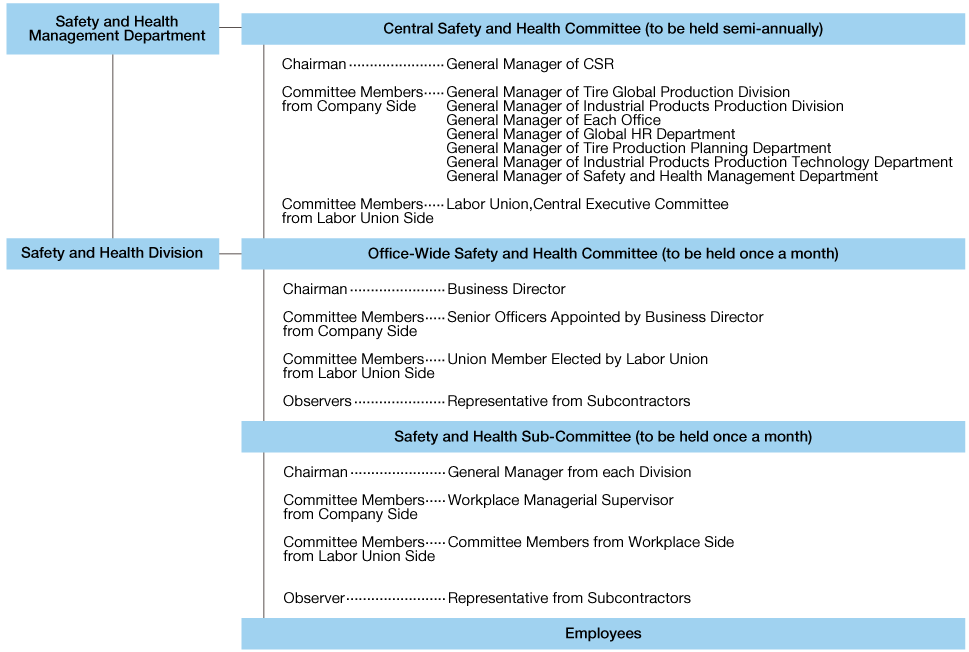
Central Safety and Hygiene Committee
The Central Safety and Hygiene Committee that is held twice a year confirms basic policy and key initiatives concerning labor and management as an essential part of communications.
The following three key initiatives were confirmed with labor and management at the Central Safety and Hygiene Committee held during 2013.
- Human resources
- : Re-enforce the process of stopping, calling, and waiting. All employees should aim to become safe workers.
- Facilities
- : Faithfully conduct risk assessments and implement mapping and improvements.
- Frameworks
- : Use open work observation effectively and develop standard operating procedure documents.
Status of the Occurrence of Occupational Accidents
In our domestic operations, the percentage of workers’ leave in FY 2013 deteriorated from 0.44 to 0.59 from the previous year. The total number of leave arising from accident was eight, and one of these was a serious incident that resulted in the loss of a wrist from an extruder. Two accidents involved symptoms being worsened by mistakes in initial measures when the accidents occurred. In order to prevent such accidents, we need to conduct risk assessments to expose risks related to facilities and further accelerate the adoption of safety protection measures based on a correct assessment of risks. In order to prevent such accidents, we will promote education that urges employees to act responsibly and to continue to improve the situation by raising awareness of safety and gaining an understanding of correct emergency measures such as proactively stimulating various activities at each workplace. Examples include visualizing our activities by using a safety activities board. From now on, we will continue to make improvements to leverage our awareness levels by identifying potential risks as well.
* Percentage of workers' leave = (number of the case of occupational accident / total work hours) x 1million hours
* Every piece of data is an aggregated value per year (from January to December)
* All industries (excluding general construction industry), manufacturing industries are based on "Survey on Recent Occupational Accidents"; statistics announced by Ministry of Health, Labour and Welfare
Frequency of Occupational Accidents (Percentage of Workers' Leave)
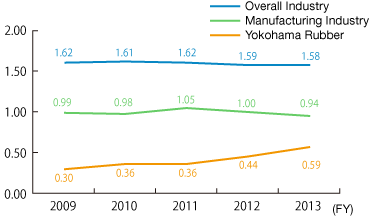
Six Pillars of Approaches Aiming For Safety Workplace
Yokohama Rubber Group is conducting six pillars of approaches in our domestic and overseas operation sites in order to fortify safety and accident prevention even further. Also, we have conducted "Corporate-Wide Convention for Safety and Accident Prevention" nine times for entire domestic operation sites grouped together, pledging to "aim for a workplace environment without any existence of risks" as an entire corporation as a team by sharing various activities with regards to safety and health, plus accident prevention from each operation site.
1. Establishment of Occupational Health Safety Management System
Out of the strong intention by our management to aim for the establishment of organization systems or management systems in order for our operation sides to duly fulfill to bring about total zero risks, we are trying to get each of our offices to obtain the certification of Occupational Health Safety Management System (JISHA/OSHMS); as a result, nine of our offices were able to obtain as of 2012 (six domestic offices in FY 2011, one domestic office and two overseas offices in FY 2012). Occupational Safety and Health Management System (OSHMS) certification was also acquired for six office overseas.
In addition, in order to assess the strengths and weaknesses of each business location and promote improvements, we will establish company-wide shared audit items and the Safety & Health Management Department will conduct a safety diagnosis once a year and provide support in response to insufficiencies to strengthen and encourage safety activities both in Japan and overseas.
Example of safety diagnosis by the Safety & Health Management Department
2. Making our Facilities Safer
We have taken measures by utilizing the method of risk assessment that can be "pre-emptive management" of accident prevention, conducting identification and evaluation of any potential risks in our existing facilities, followed by prioritizing them. Also by gathering our workers’ ideas, we are creating repair tools and facilitating automation of the facilities so that they can still be processed without workers acting when trouble occurs; this is how we aim to create various facilities that ensure safety and comfort. We also focus activities on preventing major risks that could cause a significant disaster from being overlooked. The same standards that are used in Japan have been adopted for risk assessment overseas.
3. Further Enlightenment for Safety
We are trying to train our workers for good sensibility; who can foresee risks in any potential incident. We are conducting KYT (Kiken [Risk] Yochi [foresee] Training) which is to be done by every worker every day, along with sampling and improvement for Hiyari Hatto (a near accident) incident that are voluntary activities to be attended by everybody. We have also conducted training at Taikan Dojo (training through actual experience for accident prevention). Also, we have facilitated enlightenment on safety by focusing on communication like supervisor interacting with a worker one-by-one whilst understanding the meaning of each operation until they can have autonomy to conduct safe operations on their own. In addition, in an aim to further improve work and facility safety including emergencies we promote open work observation and make gradual revisions to safe work manuals from the perspective of the office organization. Through these approaches, while the ratio of safe workers (workers certified as having safety skills based on the internal criteria) at all domestic business locations was 60% as of June 2013, the ratio of safe workers was confirmed as being 75% as of December 2013 as a result of education and training provided in response to the weak points of individual workers.
Cases of hiyari hatto (near accidents; cases in which near accidents can be determined at a glance)
Activities to identify near accidents and make improvements are not conducted by just individual workers, but are conducted as company-wide activities including indirect workplaces as well.
Mapping is an example of these types of activities. A sticky note is pasted at every location mapped for a near accident. In this manner the danger points identified are visualized and many people are able to tell at a glance by the sticky notes where a near accident occurred, which leads to actual improvements. In addition, people that identify near misses provide feedback on improvement activity information.
-
Before mapping
-
After mapping (location of sticky note is where near accident occurred)
4. Creating Comfortable Workplaces
We have been proceeding with facility maintenance, improvement on work method, maintenance management in order to maintain comfortable work sites by conducting measurement of the work environment. Also, using 5S as a basis (Seiri [tidiness], Seiton [being organized], Seisou [cleanliness], Seiketsu [hygiene], and Shitsuke [discipline]), we are trying to facilitate efficient manufacturing such as required products that are safe when needed, and at required quantity only.
5. Promoting Workers' Mental and Physical Health
In order to prevent overworking or health hazard that comes from overstress, we are monitoring workers' working hours, also, we have continued providing counseling session or making improvement of work operation for our workers who engage in long hours. Also, we have set up our company's preventative management and placed a counseling care as our activities for workers' mental health. Furthermore, we are conducting special health screening as well; we have continued giving medical guidance for those who are subject to special medical guidance. Going forward we will gain an understanding of the situation overseas and implement mental health measures.
Establishment of Measurement as to Working Long Hours and No Overtime Work Days
We are trying to shorten working hours by specifying the days for workers to go home without any overtime work; this is determined by our each office.
Also, when the special provisions as to Overtime Work Agreement were to be applied, both labor and management sides verify the legitimacy in advance, make sure such overtime work cannot be habitual from now on; we are also conducting a hearing session along with future improvement plans.
Changes of our Average Overtime Work Hours
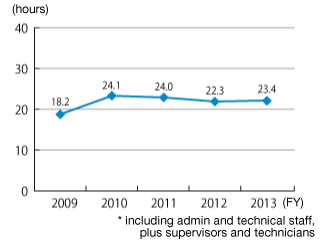
How to Deal with our Personnel who are Working Long Hours
We are conducting counseling by our company doctor or giving guidance according to the working hours based on our guidelines by properly managing workers' hours spent in the premises and their actual working hours.
Measurement for Workers' Mental Health
We are providing various counseling sessions by psychiatrist, specialized counselor, or counseling on the phone; we are also conducting consultation by company doctor to prevent any health hazard arise from overworking.
Counseling Support System and Program to Assist Workers to Return to Work
As for returning work for those workers on a long leave associated with mental health, we are trying to have them return by planning as follows; upon conducting hearing session with him or her in person, checking with his/her doctor-in-charge, company doctor, public health nurse, and company, followed by reviewing its method, timing, or any restriction for work. Even after their return, we are still conducting 3-party counseling by himself/herself, company doctor, and company to release any restrictions on work gradually; we are following up until it there are totally no restrictions with him/her at all.
6. Prevention of Traffic Accidents
All our sites are continually conducting traffic accident prevention activities and ride sharing drills by fortifying supporting system, functions, and activities to prevent traffic accidents especially through standing on the side of the road in traffic by holding a placard during rush hours and to identify the risk points in commuter routes. Also, we are conducting enlightenment activities under the cooperation with local police or agency related to traffic safety through means such as holding traffic safety seminars. Going forward we aim to conduct enlightenment activities concerning traffic safety overseas in accordance with the commuting conditions in each country.