Quality Policy
We contribute to society by planning, designing, producing, and selling attractive products for the satisfaction of our customers while maintaining a quality assurance system in all of our processes, including service. To this end, we will conduct systematic activities to ensure that all the basic steps in our quality assurance activities function properly.
As a contributing member of the global community, quality control is an essential element of our pledge to give first priority to customer satisfaction and to build a trusted reputation in society. According to our corporate philosophy, it is our responsibility to establish a stronger, more functional quality control and service system. We will promote quality control at our ever-expanding overseas production and sales sites, which we will continue to expand and enhance even further.
In FY 2013, we voluntarily recalled our tires for lightweight trucks in the US in order to appropriately address quality control issues. For further quality improvement, we have identified some key performance indicators (KPI) to measure our progress, and among them are “number of employees who newly-completed quality training at factories,” “number of newly-qualified service engineers,” and “total number of ISO/TS16949 qualified internal quality auditors.” We have implemented training programs for service engineers who can serve from the customers’ point of view, workshops at our sales bases, and have been upgrading our education materials and programs in a systematic manner, as shown below.
Atsunori Agari
Head of the Tire Quality Assurance Division
Training for service engineers
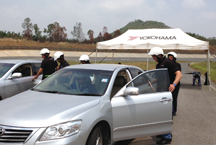
Our Tire Service Training Center in Thailand was established in October 2011, and since that time has been conducting training programs for service engineers, to enable them to provide more practical service from the customer's perspective. Participants are able to deepen their understanding of basic knowledge and learn the latest information about the production of tires, while also experiencing various issues in an actual car on test drive courses so as to learn how to improve those issues.
Company-wide debriefing session for the prevention of recurring quality issues
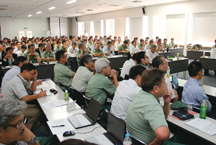
We held a company-wide debriefing session, which included relevant overseas divisions, on the prevention of recurring quality issues, overseen by Global Quality Assurance (company-wide quality and technology service).
We will continue to develop our global activities to improve customer satisfaction by sharing quality information.
Complaint handling and training for agencies
YOKOHAMA EUROPE GmbH (YEU) Technical Service
We have opened an online contact window on the YEU website to accept queries and claims about our products, including tires. We also have a division to handle quality-related claims from European agencies, which manages, aggregates, and analyzes all of the complaints. Also, aiming to provide the best products and to prevent troubles by providing appropriate advice to our customers, we proactively provide training programs at various levels, from basic training for sales representatives to advanced training for technical staff in Europe.
Lectures at sales bases and enhancement of the global quality assurance system
In our Multiple Business Group, we hold lectures on product knowledge and handling by experienced engineers who have been appointed in a sales company or sales base. They work to enhance communication for human resource development and to develop activities for prompt customer service. We held 34 such lectures in FY 2013.
We have determined a quality assurance rule to clarify responsibilities and authority, from product planning to the after-sales quality assurance system, at factories in North America, Europe, China, Taiwan, and Thailand. In order to realize universal quality, the rule has been utilized as an educational tool for quality assurance for both appointed and local staff.